WHAT MAKES LASER WELDING SO ATTRACTIVE?
90% TIME SAVINGS*
65% COST SAVINGS*
* = compared to Manual MIG Welding
Why are more manufacturers switching to welding with fiber lasers from traditional welding techniques?
Staying competitive today requires cost reductions, efficiency gains and repeatable part quality that cannot be met by traditional techniques that rely on increasingly scarce, highly-skilled craftsmen. Enabled by unprecedented no-maintenance, high-reliability and low-cost fiber lasers, fiber laser welding systems have become the preferred welding solution for the manufacturing industry.
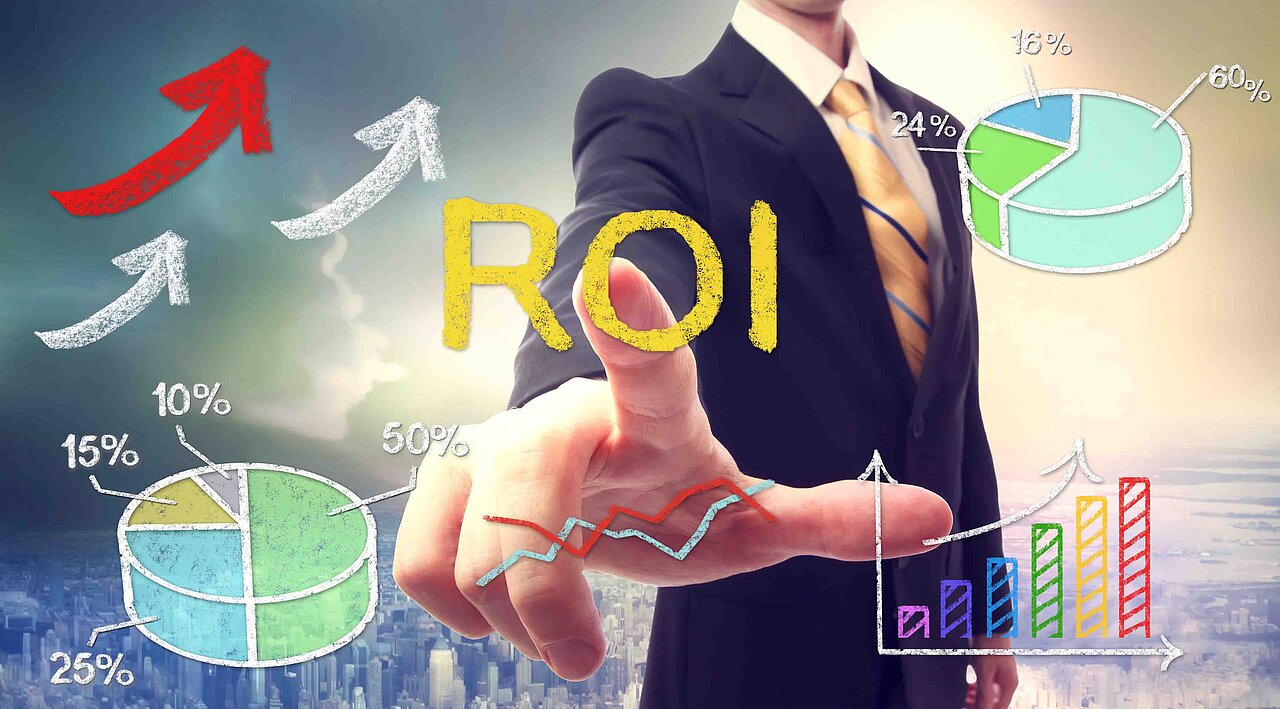
Why choose a laser welding machine?
Laser welding machines have several advantages:
They are very fast:
-
The laser allows the metal to be heated extremely quickly, while limiting the risk of deformation.
-
This technology is particularly effective for welding large quantities of sheet metal and is therefore widely used in the automotive industry.
They are also highly accurate:
-
They allow a localized, very fine, very clean, almost invisible welding.
-
They are particularly suitable for welding small parts.
-
This type of welding is very popular in the dental and jewellery industries as it provides the most aesthetic welding possible.
-
It is also possible to split the laser beam into several beams to provide welding that is even more accurate.
They can be adapted to a wide variety of part shapes and materials:
-
Laser welding machines are mainly used to weld metals, including refractory metals.
-
It is also possible to weld non-metallic parts with them, such as porcelain and glass.
-
You can use them to weld parts with very different shapes.
They do not wear out:
-
Laser welding machines operate without contact, so there is no risk of wear and tear on the machine.
-
There is also no need to change tools or electrodes, which is a definite advantage in terms of waste reduction.
They can be given orders digitally:
-
It is now possible to control the quality of the welding from a computer during the welding process.
-
The high level of automation allowed by such a process also makes it possible to detect and solve any quality problems.
They are VERY affordable
-
Fiber laser welding is now with our Lasermach WOBBLE Handheld fiber laser welding machine VERY affordable and accesable for every company
This is why all manufactureres switch to fiber laser Welding
Gas Metal Arc Welding (GMAW) vs Fiber Laser Welding
GMAW or MIG is a traditional technique using a consumable electrode that works well for larger, badly fitting parts.
-
Fiber laser welding does not use consumable electrodes, requires less edge preparation, is easily automated and is up to 5x faster.
-
Fiber lasers also provide more precision, and lower heat input.
Gas Tungsten Arc Welding (GTAW) vs Fiber Laser Welding
GTAW or TIG uses a non-consumable electrode and provides better process control than GMAW but any filler has to be added separately.
-
Fiber lasers are up to 10x faster with higher precision, lower heat input, and are more easily automated.
Plasma Arc Welding (PAW) vs Fiber Laser Welding
PAW is faster than GTAW, but much slower than laser welding. Having a large melt pool, PAW is good for badly aligned parts, but creates too much heat for many applications.
-
Fiber lasers offer higher precision, are faster, and have lower heat input in a non-contact process.
-
Laser Wobble Welding is as effective on misaligned parts and does not require daily maintenance of the process head.
Resistance Spot Welding (RSW) vs Fiber Laser Welding
RSW is typically used for joining two pieces of material that are stacked on top of each other.
-
Fiber lasers only need single-side access, are much faster, and produce higher-strength welds.
-
Fiber lasers do not require electrodes and eliminate the costs and time for electrode replacement.
Electron Beam Welding (EB) vs Fiber Laser Welding
EB welding provides excellent weld quality and a low heat affected zone. Because the process is in a vacuum chamber, contaminant levels are very low.
-
Fiber laser welding speed is similar to electron beam, but because lasers do not require part transfer through a vacuum chamber, laser cycle time is dramatically shorter.
Our Wobble fiber laser welder gives you back the POLE position!
We beat them ALL
Comparison welding | Traditional welding | Laser welding | Wobble-3 laser welding |
---|---|---|---|
Heat input to the workpiece | Very high | Low | Low |
Deformation of the workpiece, undercut | Big | Small | Small |
Bond strength to base metal | General | Good | Very good |
Follow up treatment | Polishing | No need to polishing or rarely polished | No need to polishing or rarely polished |
Welding speed | General | More than 2 times argonarc welding | More than 2 times argonarc welding |
Applicable material | Stainless Steel, Carbon steel, Galvanized sheet | Stainless Steel, Carbon steel, Galvanized sheet | Stainless Steel, Carbon steel, Galvanized sheet |
Consumables | More consumables | Less consumables | Less consumables |
Operation difficulty | Complicated | General | Simple |
Operator safety | Unsafety | Safety | Safety |
Environmental protection impact | Not environmentally friendly | Environmentally friendly | Environmentally friendly |
Welding fault tolerance | Good | Bad | Good |
Wobble/Swing welding | No | No | Yes |
Spot width adjustable | No | No | Yes |
Welding quality comparison | Bad | General | Good |
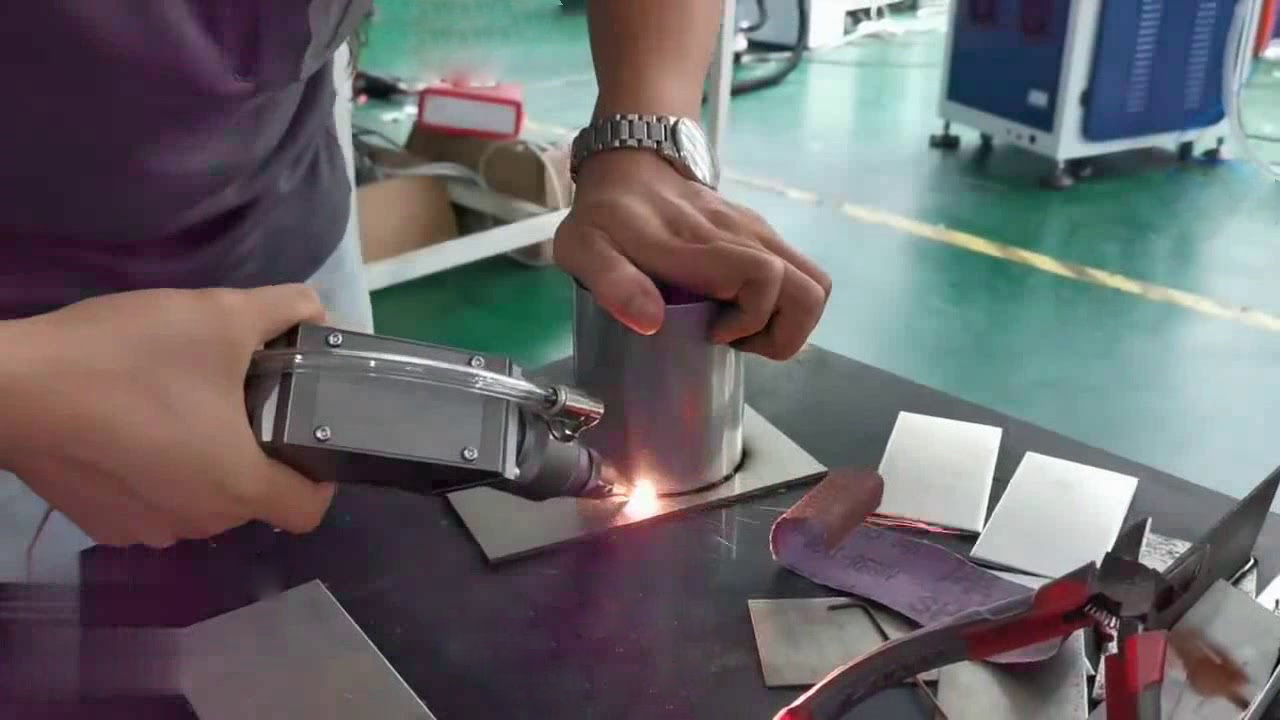
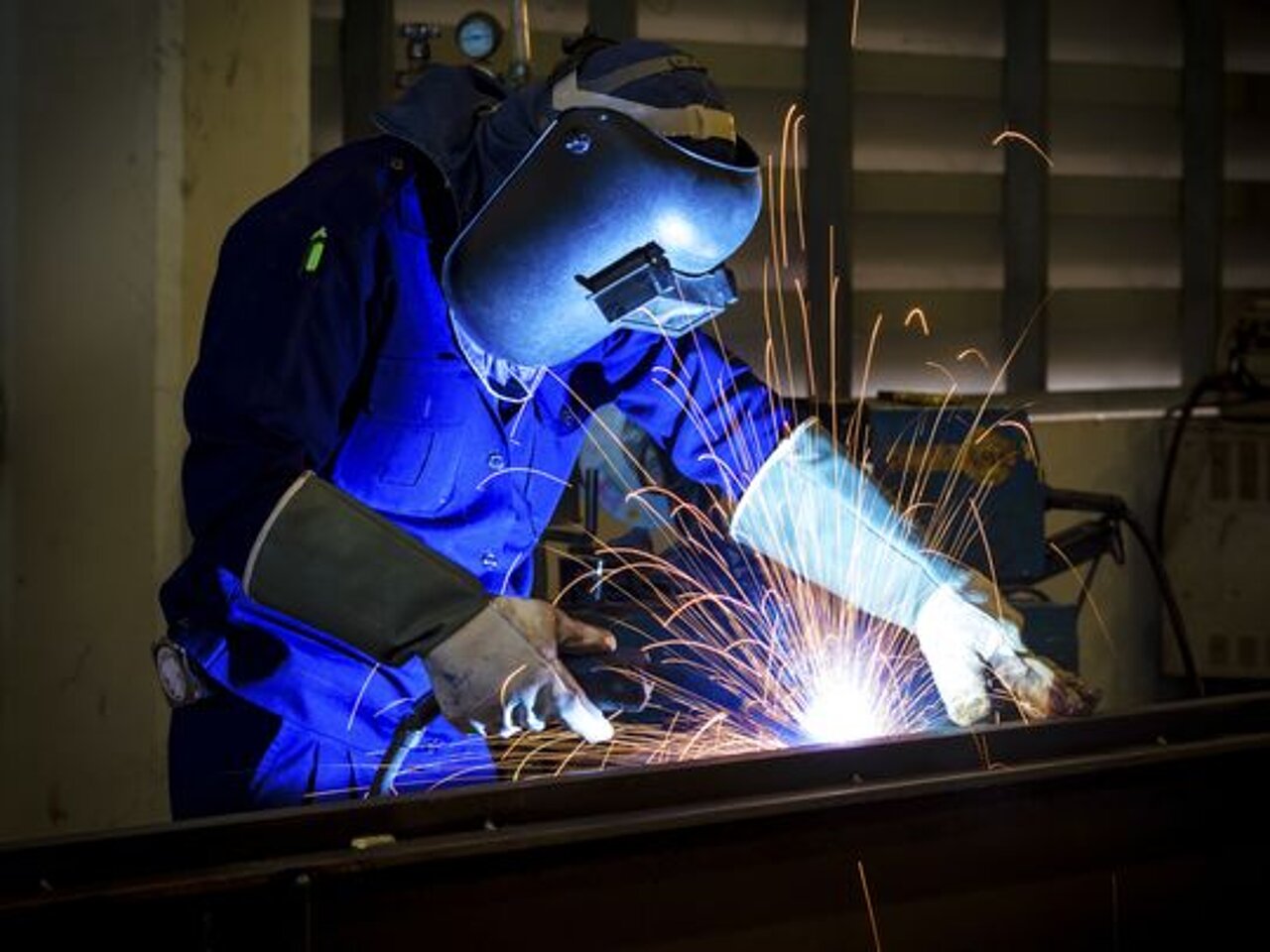
We don't talk about this: Peoples Safety, Peoples Health, Peoples Workload
Simply look to the pictures and make your own conclusions!! We hope you see some differences that can interest you!!
How to choose the laser beam source?
There are three types of sources: fiber laser, CO2 laser and Nd:YAG laser.
The choice of source depends on the type of laser you have chosen (pulsed or continuous).
- The fiber laser:
- This technology is based on sharp and thin beams that allow continuous and penetrative work to be carried out.
- Like the CO2 laser, the fiber laser can penetrate thick sheets with great speed and efficiency.
- It is easier to integrate into a machine than other lasers both in terms of use and maintenance.
- This laser offers an average efficiency of 30-40%.
- The CO2 laser:
- This technology uses a gas mixture of carbon dioxide, helium and nitrogen that is electrically-excited and optimized for continuous operation.
- Like the fiber laser, the CO2 laser can penetrate thick sheets with great speed and efficiency.
- It is more effective at penetrating thick steel parts than the fiber laser so it is more widely used.
- It is more flexible and can penetrate thicker and lighter materials than the fiber laser.
- This laser offers an average efficiency of 7%.
- The Nd:YAG laser:
- It allows effective control of the power, duration and shape of the laser pulses.
- It is optimized for pulsed mode.
- But it emits pulses of very different wavelengths that do not all reach their target and then dissipate in the form of heat.
- This type of laser has the lowest energy efficient : 3~4%
FIBER laser is the WINNER
TOP Advantages of Fiber Laser Welding Technology
Highest Part Yield
The high stability of the laser power and beam profile of the IPG fiber laser ensures a very repeatable process that delivers the same high-quality weld every time. This non-contact process with no wearing surfaces ensures the last part you produce is the same as the first.
High Throughput
The inherently high speed of laser processing combined with the ease of high-speed automation and elimination of most post-processing steps provide significantly shorter cycle times than competing technologies. Factor in the high-yield process, and IPG fiber laser welding delivers more good parts faster than alternate joining techniques.
Fast ROI
Together with higher-speed and lower-cost processing, the high uptime and availability of the laser welding system enabled by the zero-maintenance fiber laser make for the lowest cost per part welding, and the fastest return on investment.
Fiber Laser Welding
Lasers provide contact-free, high-speed metal welding solutions for advanced manufacturing across countless industries.
With fiber lasers, laser welding has become a highly reliable, easily automated process that provides the highest part quality, typically at the lowest processing costs, and virtually maintenance free.
- High-precision accuracy for joining even small parts
- Low heat input for minimal distortion
- Non-contact welding - no degradation in welding quality
- No current passes through the part
- Weld dissimilar metals (e.g. Cu to Al)
- Minimal maintenance – high tool availability
- Easily automated for high-productivity, high-yield manufacturing
High speed laser welding produces high part yields at low operating costs that results in the lowest cost-per-part
FIBER LASER BENEFITS
The fiber laser has the following benefits and advantages:
1. When compared to CO2 laser beam, it provides simplified beam delivery using fiber-optic cables without having to deal with alignment of mirrors.
2. It is absorbed more by metals, especially good conductors, and is less absorbed by plasma vapours formed above the weld pool.
3. Fiber lasers give increased power intensity owing to its ability to be focussed to smaller sizes.
4. Light can be easily transferred to a movable workpiece because it is already present in a flexible fibre. This fact is extremely useful for laser cutting and welding.
5. Optical fibers can be several kilometers long, hence fiber lasers are capable of providing extremely high power output.
6. Large surface area to volume ratio accounts for continuous power output due to efficient cooling.
7. Fiber lasers are very stable with respect to temperature and vibrations. Fibers protects the optical path from thermal distortion.
8. Better beam quality also give cleaner welds.
9. They have very low ownership and maintenance costs and also use low electricity. These factors allow deeper penetration and faster welding speeds in comparison to other welding processes
Improve your welding productivity and precision - contact our laser welding engineer to learn how.
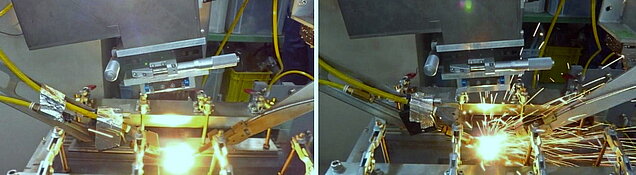
Visual comparison of projections during fiber laser welding
Welding with a laser beam reduces spark projections by 95 percent
Wobble: This new fiber laser welding technology reduces molten metal (spatter) by 95 percent or more. While traditional welding with very high projection levels can lower the quality and speed of the welding, new low-projection fiber laser technology with wobble, increases the quality and productivity of high-power fiber laser welding for industrial applications such as steel processing, automotive production and electrical equipment installations.
SPARKING COMPARISON
Left our new laser wobble technology and right the conventional welding technology in the same setup.